The key safety principles that drive the success of the Flight Operations team at Iris Automation
Iris Automation relies on the testing of our Detect and Avoid technology, Casia, through real-world field tests conducted by our Flight Operations team. The team is based in Reno, NV, but they have traveled to various parts of the country and conducted missions across different environments. The data collected from these flights is valuable for the verification and improvement of our computer vision-based Casia. With each new update and integration, there is a team of pilots and technicians out in the field flying our fleet of unmanned aircraft, testing the validity of the system.
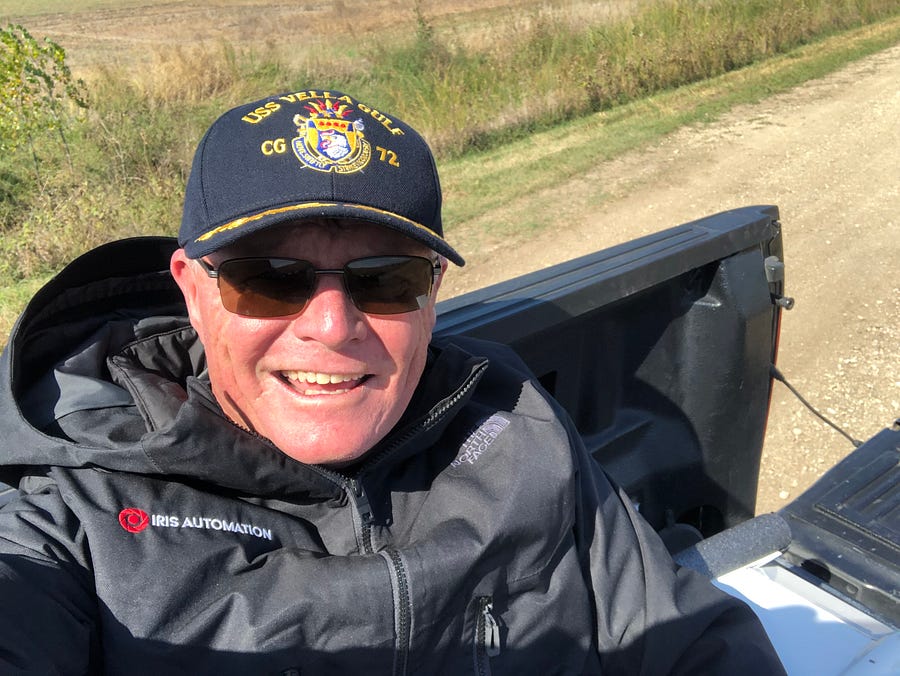
The team is led by Mark Genung, Director of Flight Operations. With over 30 years of military experience operating Navy ships and aircraft at sea, Mark knows the importance of safety and efficiency. He is responsible for the safe execution of the flight missions, from routine technical tests to planning intercepts between our equipped drones and General Aviation aircraft. Mark has determined that the continued success of the Flights Ops team is due to following what he calls The 3-Legged Safety Stool. We will break down each “leg” seen as an essential component of this policy.
“Like any three-legged stool, if one leg is removed or cut off – the stool is compromised”
1 | Highly Trained and Qualified Personnel
The success of the team is dependent on each individual bringing the best of their training and experience. Iris seeks responsible and passionate members who are comfortable with adapting to situations prone to environmental or technological change. All Iris pilots are certified by the FAA, which includes both our General Aviation (GA) and Remote pilots. General Aviation handles the flying of small private aircraft used for the intercept testing of Casia, while Remote pilots operate the various drones in the Iris fleet and the systems they run on (including Casia).
Mark explains, “All our pilots are also Remote Pilots who receive sUAS training and must qualify on each aircraft model Iris flies. Finally all receive advanced training in how to use our DAA technology and fly our data collection test patterns.”
Our Chief Pilot, Ryan McMaster, is a qualified Remote Pilot and flight instructor who has developed a curriculum for GA high density altitude flight operations while safely flying precise flight paths. This provides a guideline and ensures safety for both our personnel and equipment when we have tests designed to have drones in very close proximity to low-flying aircraft. The drone industry has grown and adapted according to regulations and innovation. The Iris Flight Ops team is constantly working to keep up with the latest developments, as seen in their participation in historic FAA-approved flight tests.
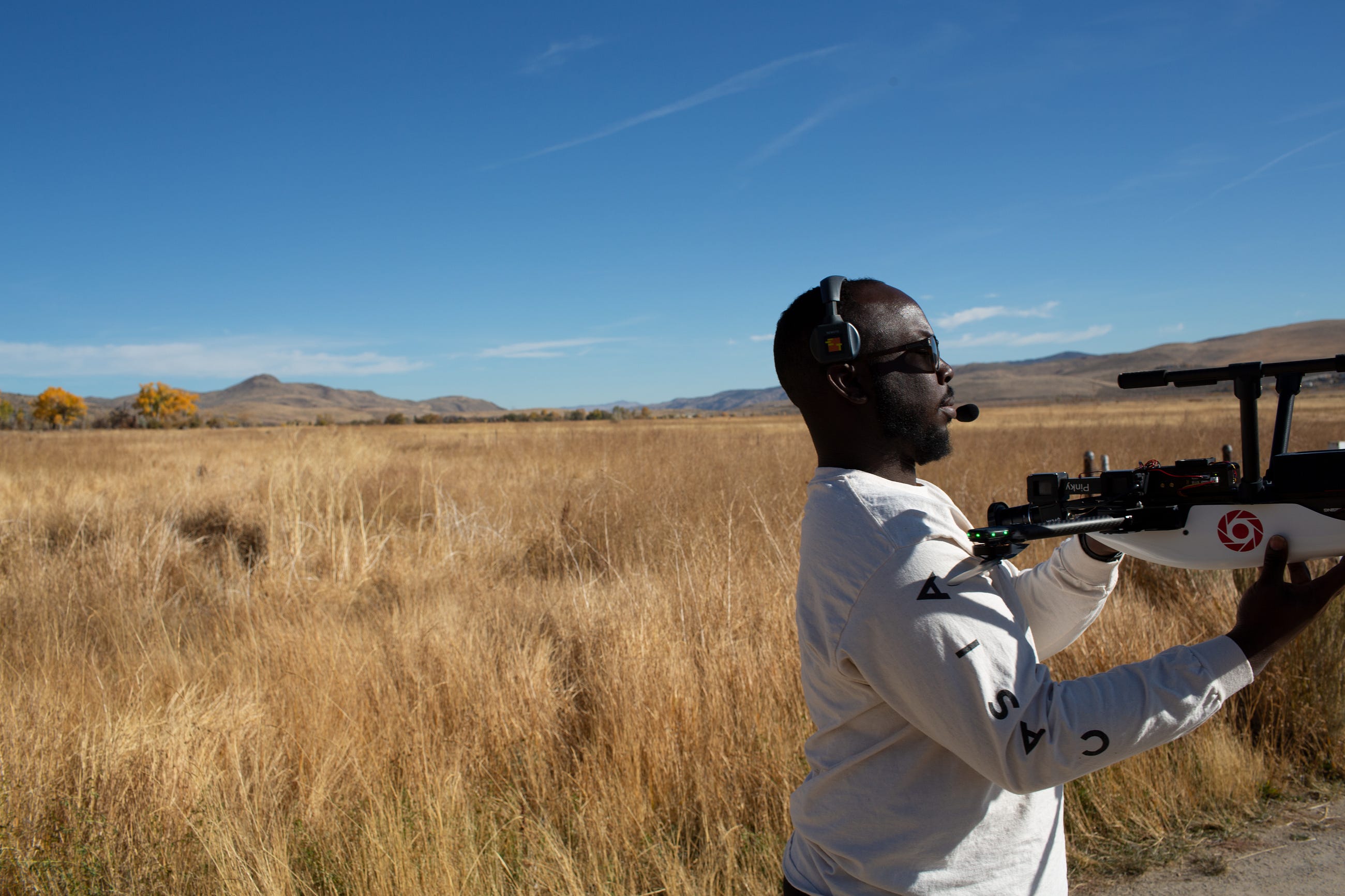
2 | Well Maintained Equipment
Casia has flexible integration with unmanned vehicles, meaning that it can be attached to any drone according the needs of the user. In some situations one might need a multi-rotor drone and in others, a fixed-wing drone. The Flight Ops team is trained to operate and maintain multiple small unmanned aircraft system (sUAS) models. This provides validation for Casia’s application across a wide-range of functions, as there is no requirement for what aircraft our partners and customers choose to integrate with.
“Each of our qualified pilots is assigned a sUAS model to maintain, upgrade and integrate. Our first line of defense is our robust pre-flight checks that ensure all aircraft subsystems are working properly before flight.”
Many of the field tests are conducted in remote locations, therefore it’s crucial that the equipment is up to capacity so that reliable data is collected. To keep a high operational availability, the team brings two or more models of the same aircraft to the field in case there is a failure with one sUAS. The team usually flies about three days a week, and this routine allows time for preventive and corrective maintenance. When a test is completed, the team immediately logs and plans to fix any equipment errors so that they can be addressed in time for future flights.
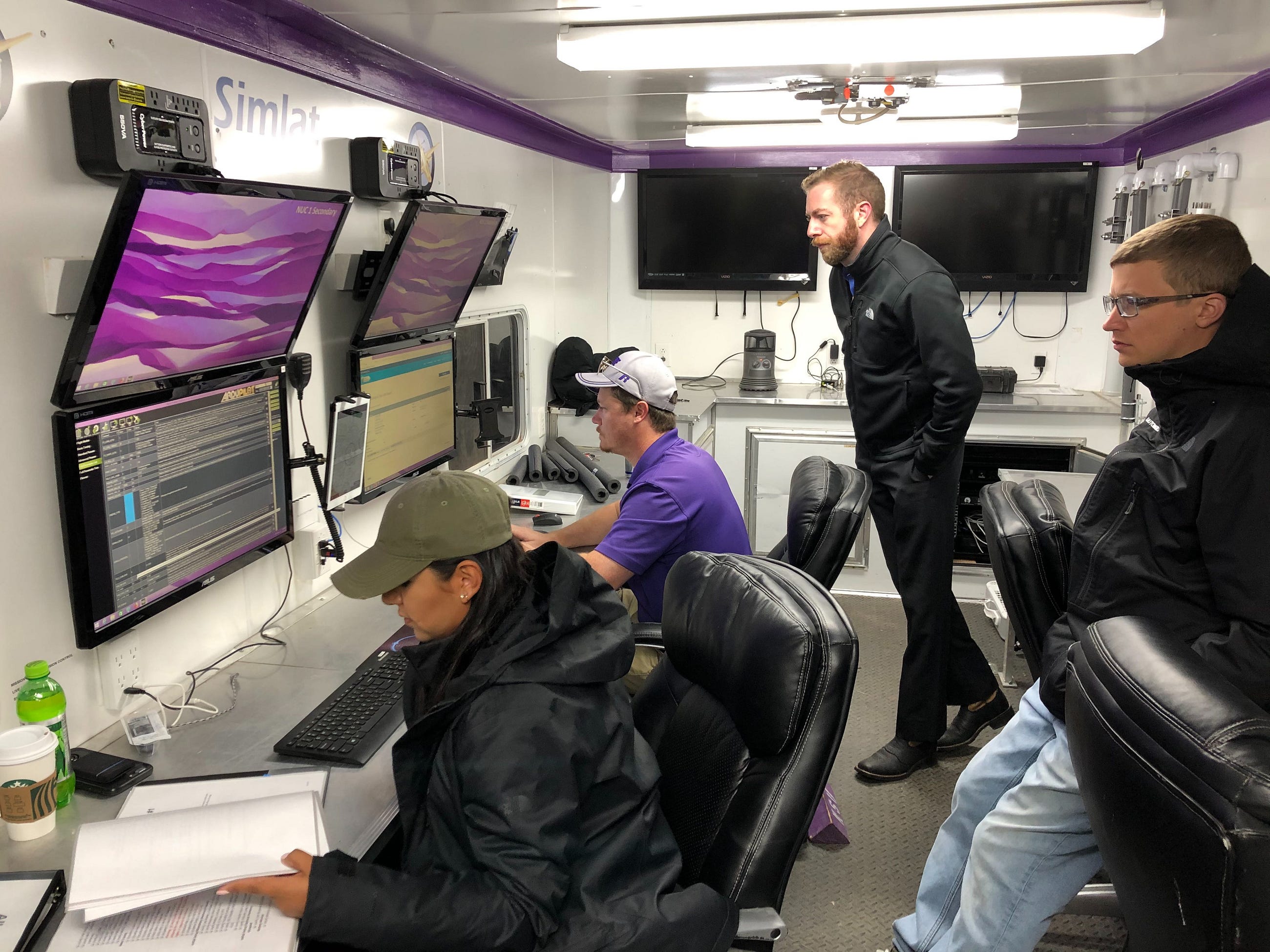
3 | Validated and Proven Operating Procedures
It is pivotal that the team conducts operations according to our Iris Flight Operations Manual (FOM). This brings a proven and tested structure so that current members have the necessary guidelines to follow. This also becomes a resource for future team members so they can easily adapt. When dealing with different systems, environments and personnel, it’s important that there are procedures to follow so that the operational mechanism continues forward in a safe and detailed manner. Mark explains just how in-depth the procedures are:
“The FOM lays out personnel requirements, equipment lists, communication protocols, operational risk management, general and emergency procedures. Each aircraft model has an individual set of Standard Operating Procedures. These procedures include sUAV capabilities and limitations, pre-flight and post-flight procedures, and specified emergency procedures.”
Before any drone takes off, there are strict protocols that the pilots and technicians must follow. Many procedures follow those provided by the Original Equipment Manufacturer (OEM), as well as those applicable to the Iris mission goals. There are Ground Control Stations used across our fleet to assist in training and to also minimize any confusion across sUAV models. Having a regular schedule of flight tests allows for the team to learn new situations and environmental conditions. Procedures are updated and revised as new information is available and developments occur.
Our safety program is based on focusing on all three of these components. Iris Automation is committed to safety, not just in the sense-and-avoid function of Casia, but in the flight testing operations that make it all possible.